Production network for the future.
To mark Battery Day, we present a few examples of how the BMW Group is preparing its production facilities worldwide to deliver electrification – and creating tomorrow’s mobility.
“Climate protection matters today, not just tomorrow,” said BMW Group CEO Oliver Zipse. And it’s just one of the reasons the BMW Group continues to accelerate the development of e-mobility significantly. In 2023 the BMW Group aims to have 25 electrified models on the roads, half of them fully electric. And by 2030 vehicles with an electrified drive are expected to account for about half of all BMW Group sales in Europe. To realise these ambitious goals, the company is developing its all components of its BMW eDrive technology in-house and further increasing production capacity of electrified vehicles and e-drives.
Berlin
The close-to-series BMW Motorrad Definition CE 04 previewed at the #NEXTGen 2020 is about to become the latest addition to the electric fleet of BMW Motorrad. At the plant in Berlin work is forging ahead to ready the lines for its series production. At the moment technical upgrades and adjustments are being made to the existing high-voltage battery line to accommodate the new model, and series production is already being trialled.
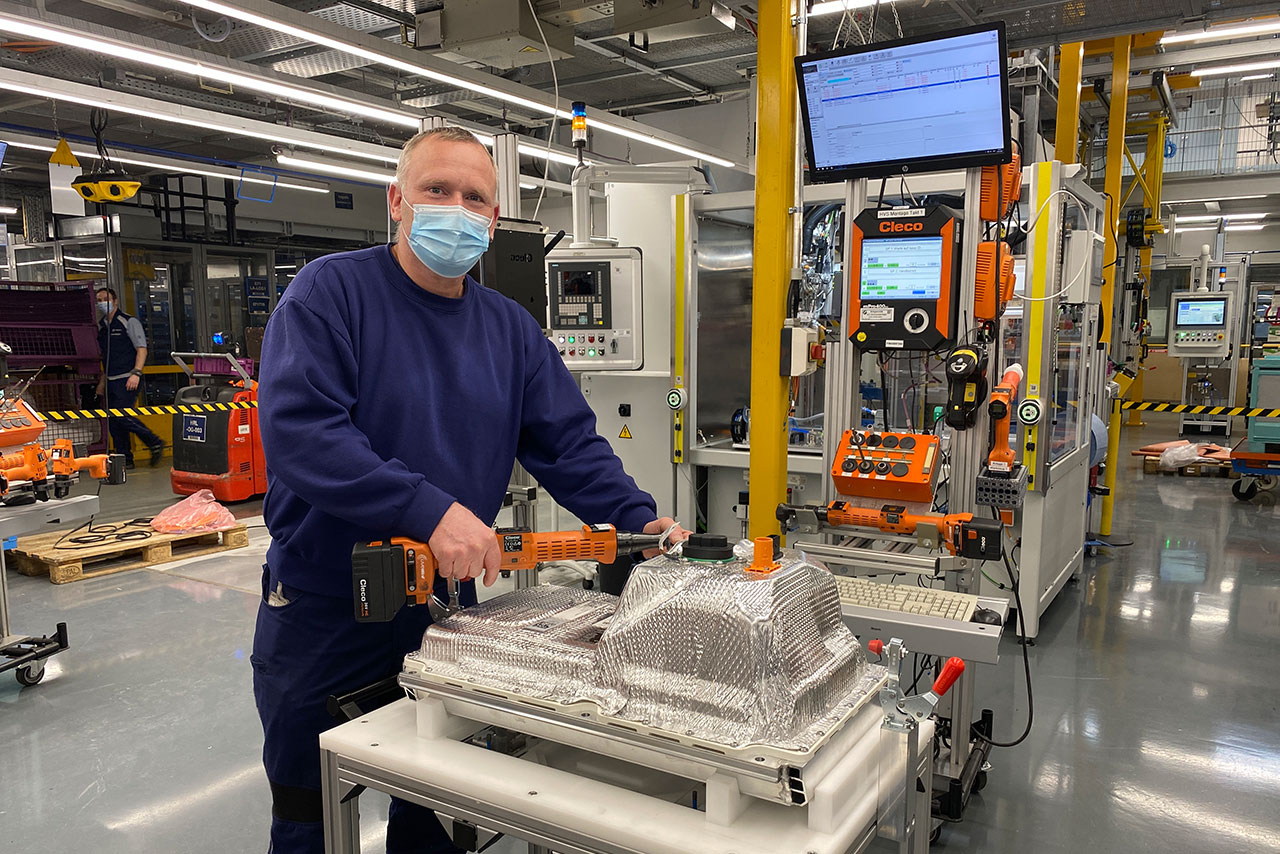
The battery of the new scooter will incorporate the latest generation of battery modules, supplied by Plant Dingolfing, and a casing manufactured in Berlin. Designed purely for electric operations, the forthcoming model will be an enhanced variant of the BMW Motorrad Concept Link. In keeping with the motto “Plugged to Life”, it will meld the analogue with the digital to become a means not just of transport but also of communication for urban commuters.
Dingolfing
With more than a decade of experience in high-voltage battery production, Plant Dingolfing has a wealth of expertise. It all started with e-drives for the BMW ActiveHybrid models and BMW ActiveE, and progressed to series production for the BMW i3 from 2013 on. Over the years, Plant 02.20 has grown to become the BMW Group’s Competence Centre for E-Drive Production. Today it manufactures not only electric motors but also battery modules, which it assembles to create high-voltage batteries. Initially these were mainly used in plug-in hybrids, but since the autumn of 2019 they have also been powering the fully-electric MINI SE.
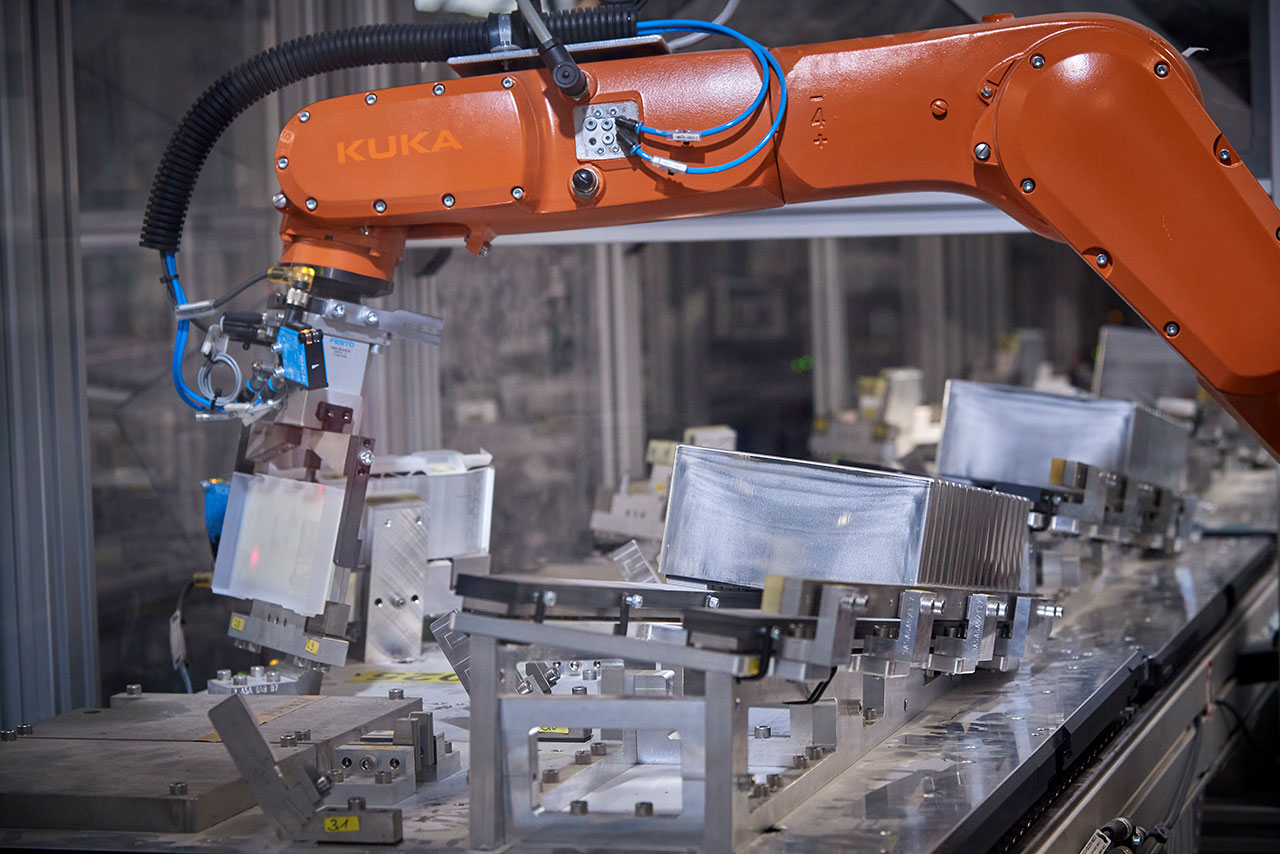
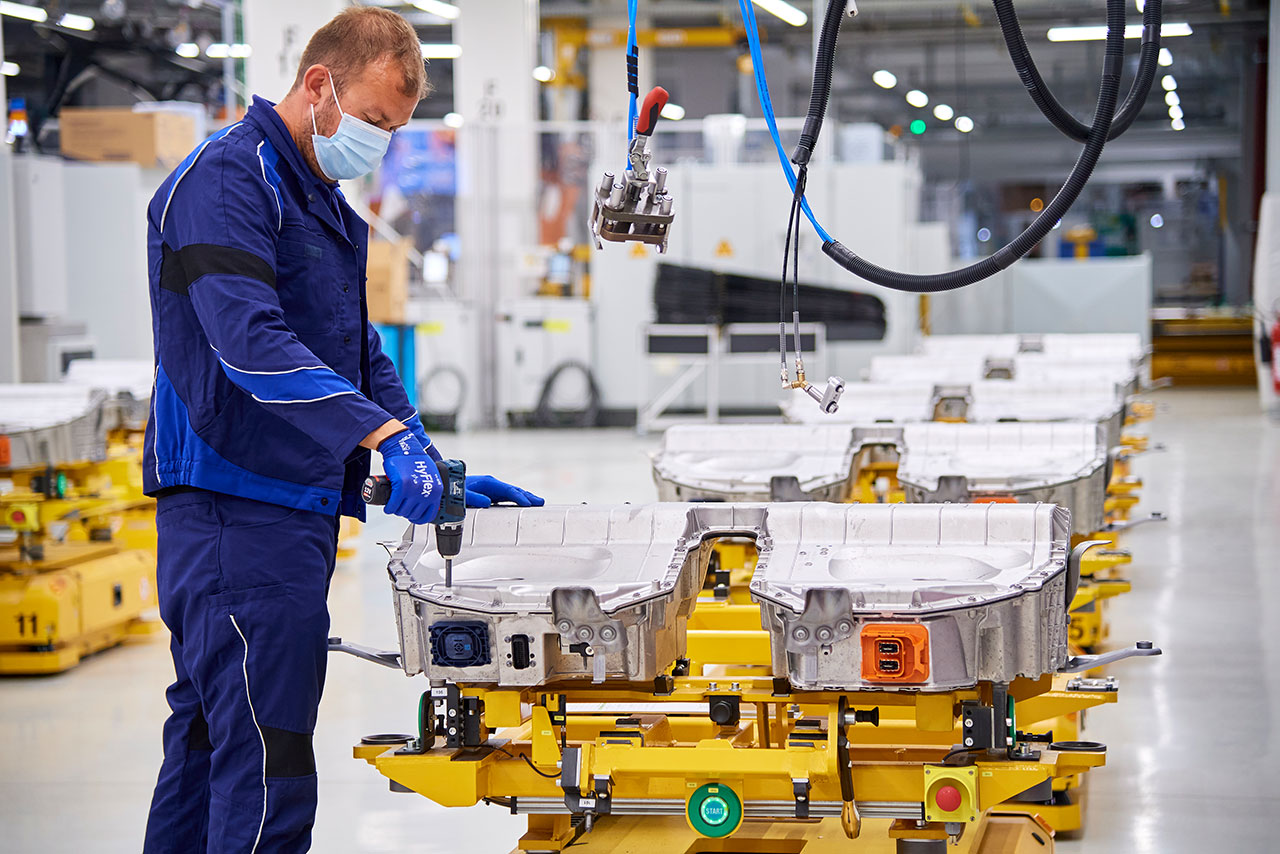
This year sees Dingolfing launch production of the fifth and latest generation of high-voltage battery, which will initially power the BMW iX and BMW i4. What’s special about Gen5 batteries is that our suppliers have committed to producing the cells for them entirely with green energy.
Landshut
When it comes to electromobility, batteries are indispensable. But so too are a great many components made at BMW Group Plant Landshut. The all-electric BMW iX, for example, is packed with innovations from there.
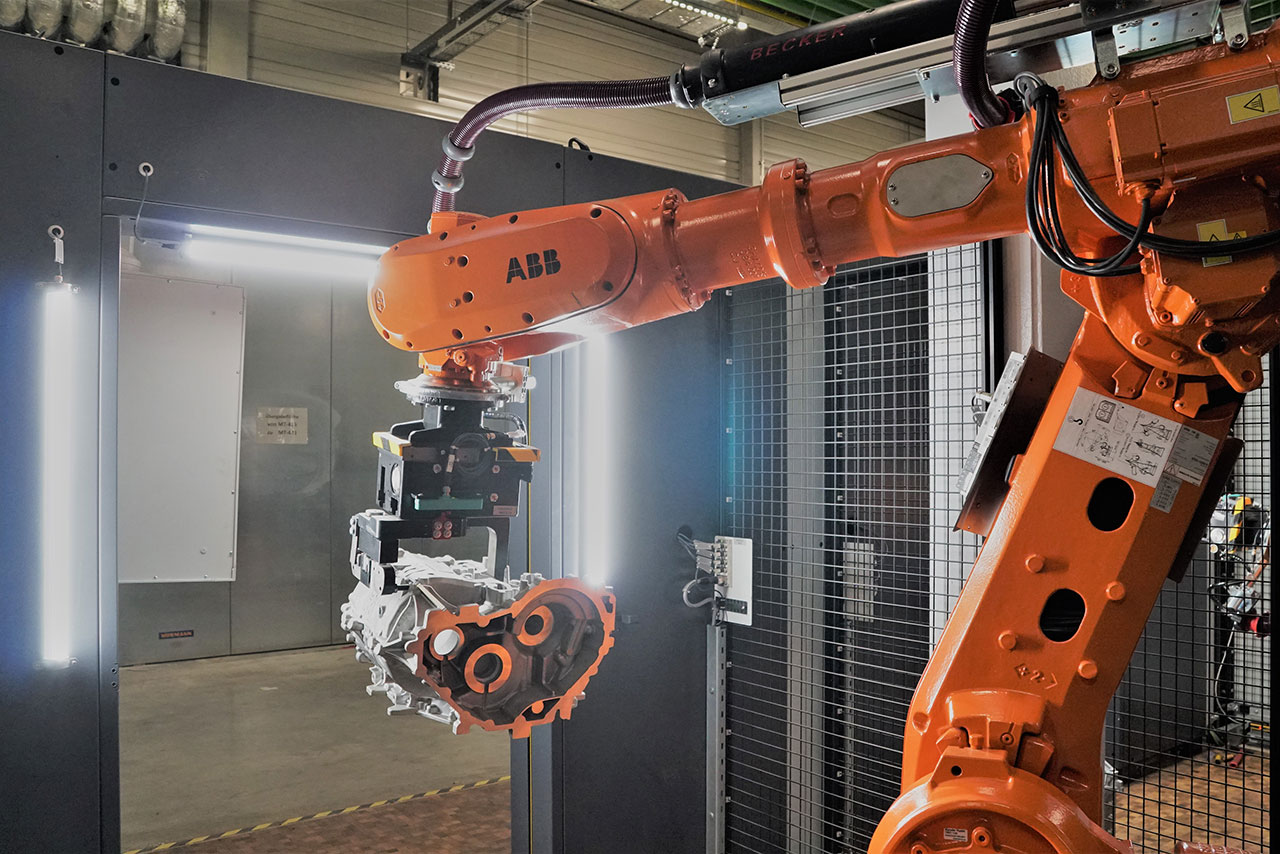
The light metal foundry in Landshut creates the casing for the highly integrated Gen5 e-drive. The casing is made of 50% recycled aluminium and injector-cast by a specially developed process (ICA) that’s unique worldwide. Incidentally, the Gen5 e-drive manages entirely without rare-earth elements.
Leipzig
The topic of batteries and electromobility is also extremely important at Plant Leipzig, which has been producing the BMW Group’s first fully electric vehicle – the BMW i3 – since 2013. In October 2020, the 200,000th BMW i3 rolled off the production lines there. The expertise Leipzig has developed over the years continues to grow and will provide important input for the manufacture of future models. The BMW Battery Farm on the plant premises gives used BMW i3 batteries a second life – as wind energy storage. The use of high-voltage battery packs can be profitable and sustainable. And the BMW Group proves it.
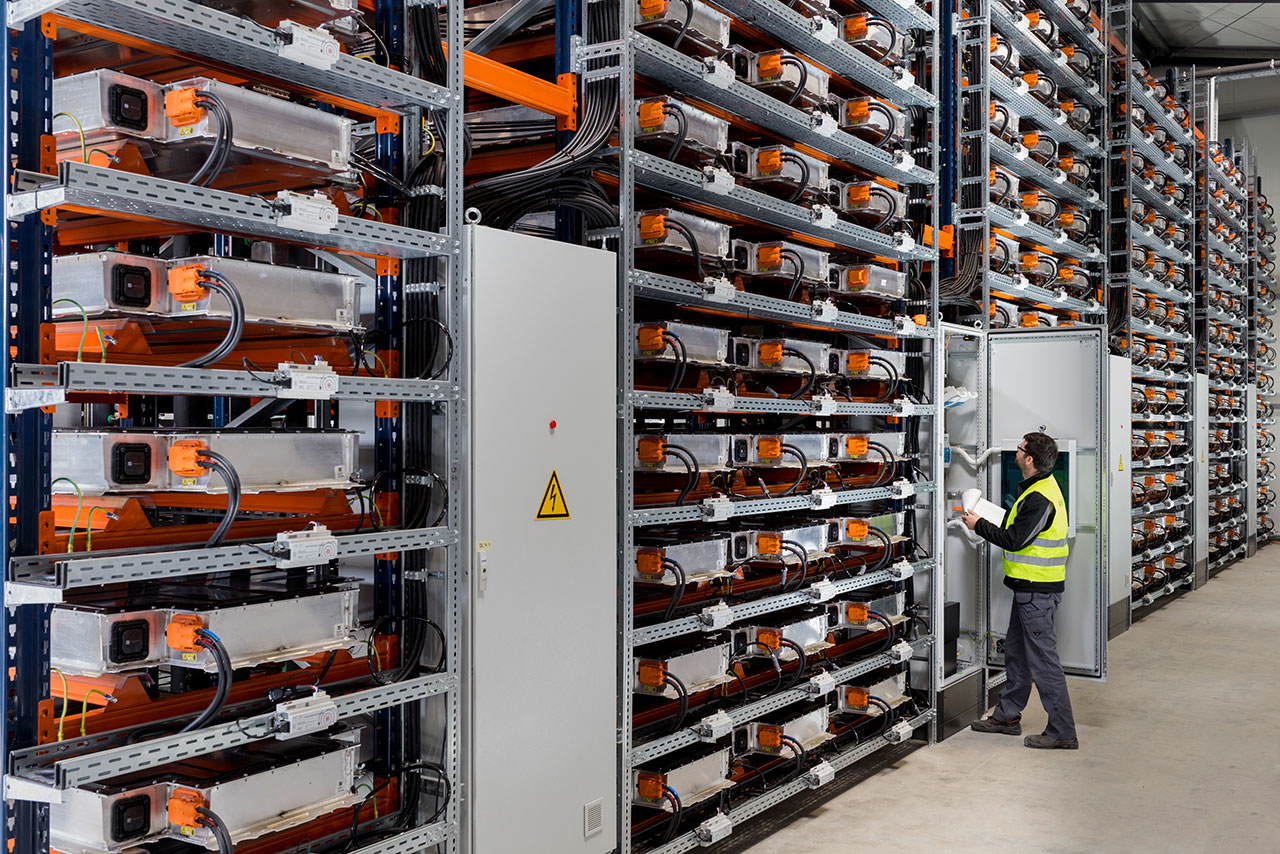
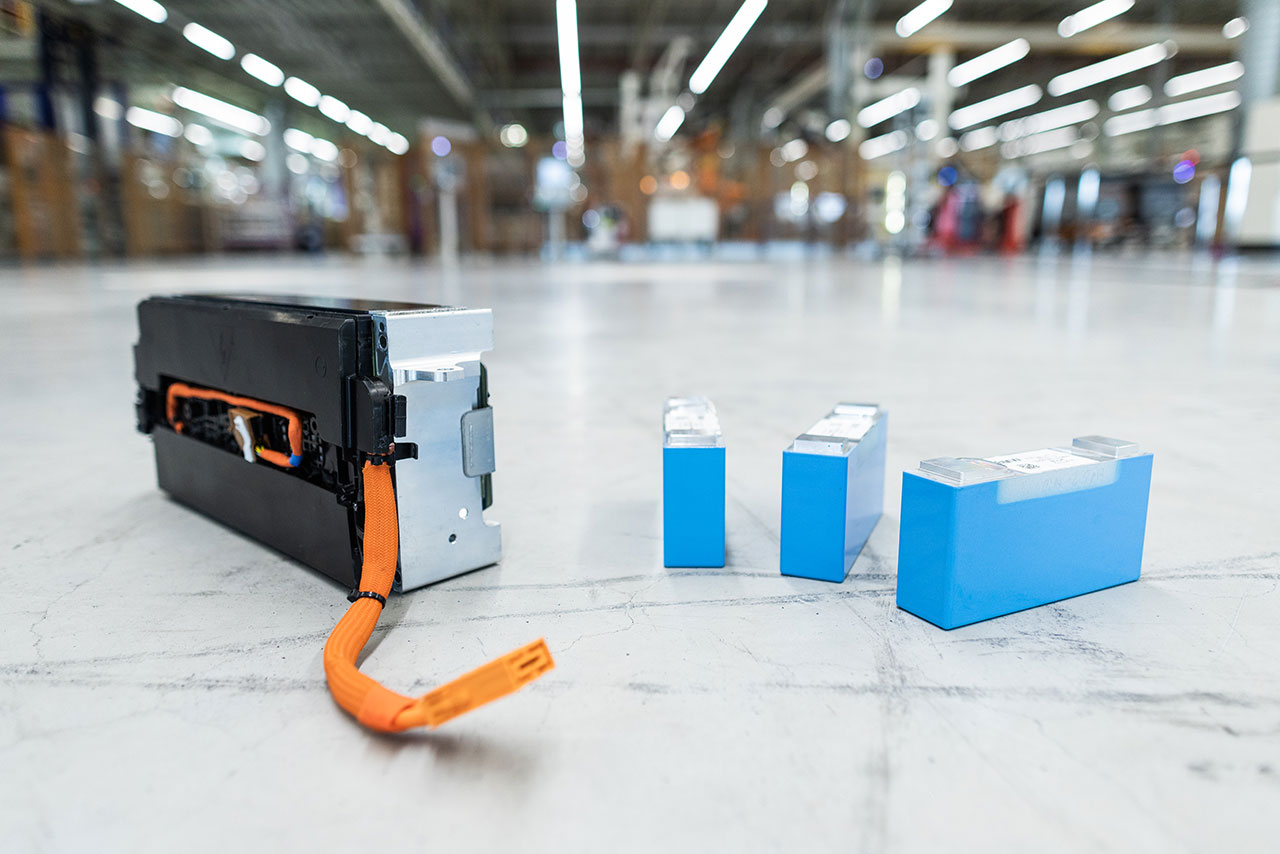
BMW Group Plant Leipzig is also headed for another milestone: the launch of a new battery module production line. The first trial run is about to begin, with series operations scheduled to start in May.
Munich
The Power of Choice: BMW Group Plant Munich manufactures the complete BMW 3 Series family with the full range of drives. The team and production processes are highly flexible and have all the training they need to give customers what they want, whether petrol, diesel or plug-in hybrid.
The plant also offers a range of training courses on working with electric drive components. Last year alone more than 300 associates signed up to take part.
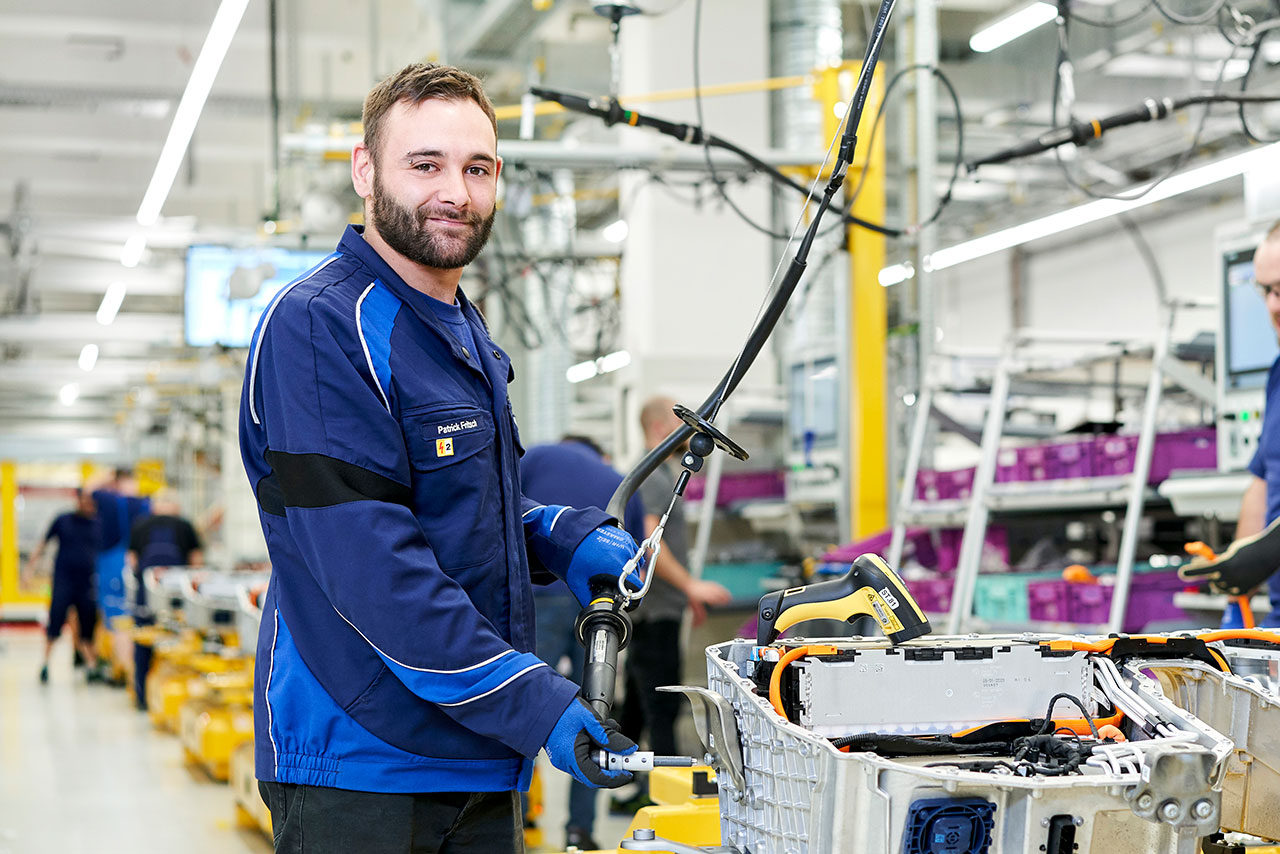
In 2021 the upskilling continues unabated as Plant Munich prepares for the production launch of the fully electric BMW i4. Another drivetrain variant for even more Power of Choice.
Oxford
MINI’s first all-electric model is fully integrated into the production process at Oxford, running down the same line as the combustion engine models. This high level of flexibility at Plant Oxford means MINI Electric production can be adjusted according to global demand. In 2020, a total of 17,580 were built at Plant Oxford and sold all around the world. This year, one in three MINI 3-Door Hatch built at Plant Oxford will be electric, reflecting the increasing customer demand for electric vehicles.
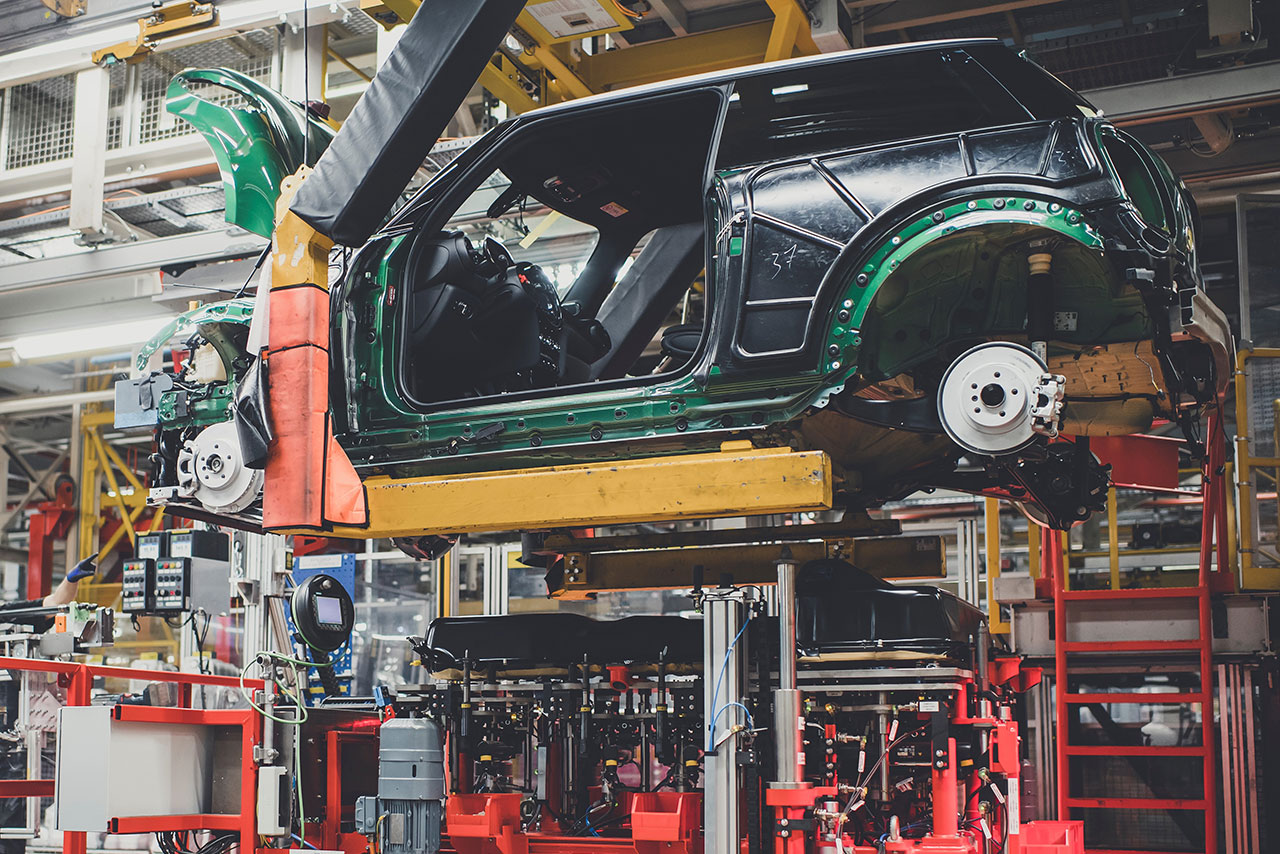
Regensburg
At BMW Group Plant Regensburg, Battery Day 2021 is Future Day. The plant is currently working on the first of several lines for applying the battery cell coating. The new system is due to go on stream in April 2021 and will make Regensburg an official member of the BMW production network for e-drive components.
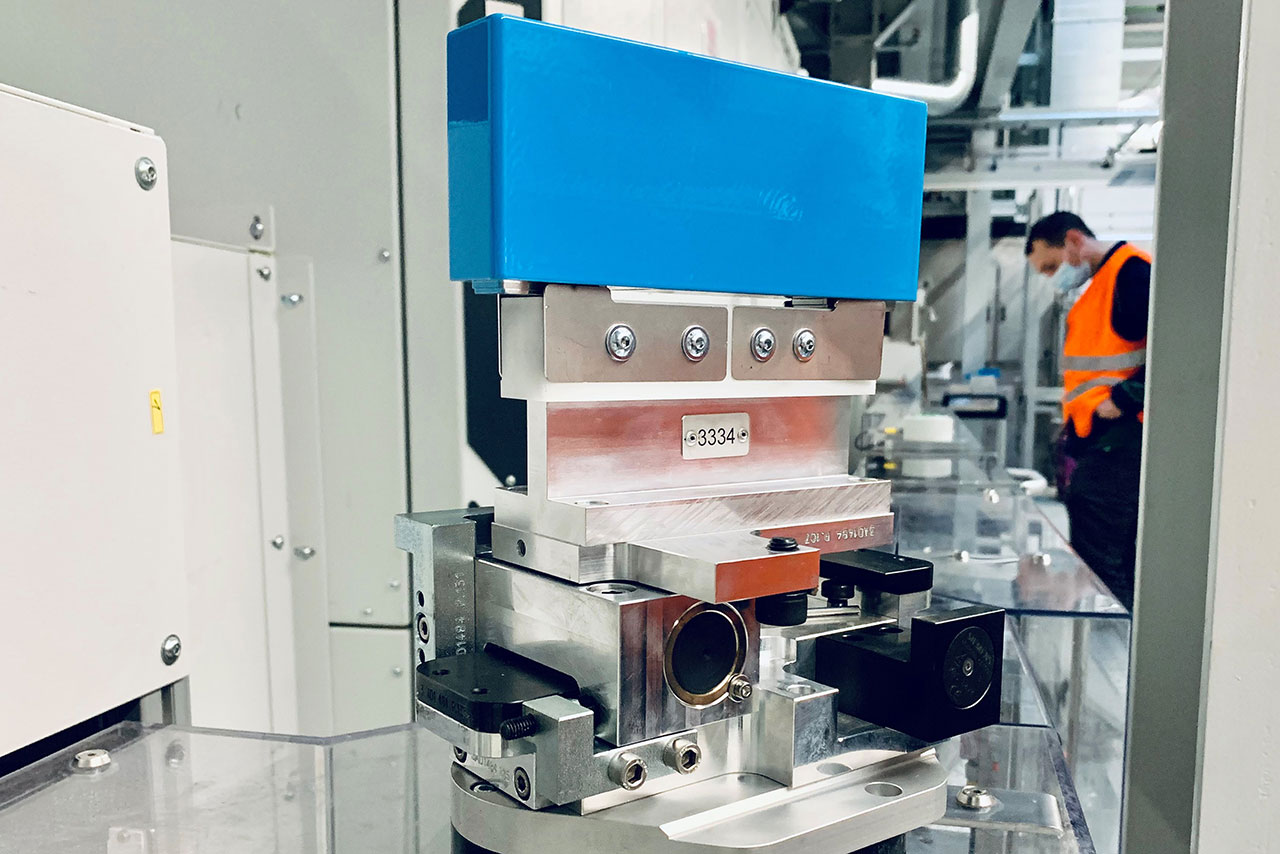
By the end of 2021 four such coating systems will be in series operation. In addition an assembly centre for high-voltage batteries will go on stream in 2022. A combined total of at least 300 new jobs with a future will be created in Regensburg.
About 50 associates are currently working hard to set up and launch the coating systems. Rather than travelling on a conventional conveyor belt, the battery cells are moved about by a fully flexible multi-carrier system – another small example of the many innovations coming out of Regensburg. The future is clearly here!
San Luis Potosí
2020 saw BMW Group Plant San Luis Potosí launch production of its first PHEV, the BMW 330e. The new generation 4.0 hybrid has more range than its predecessor.
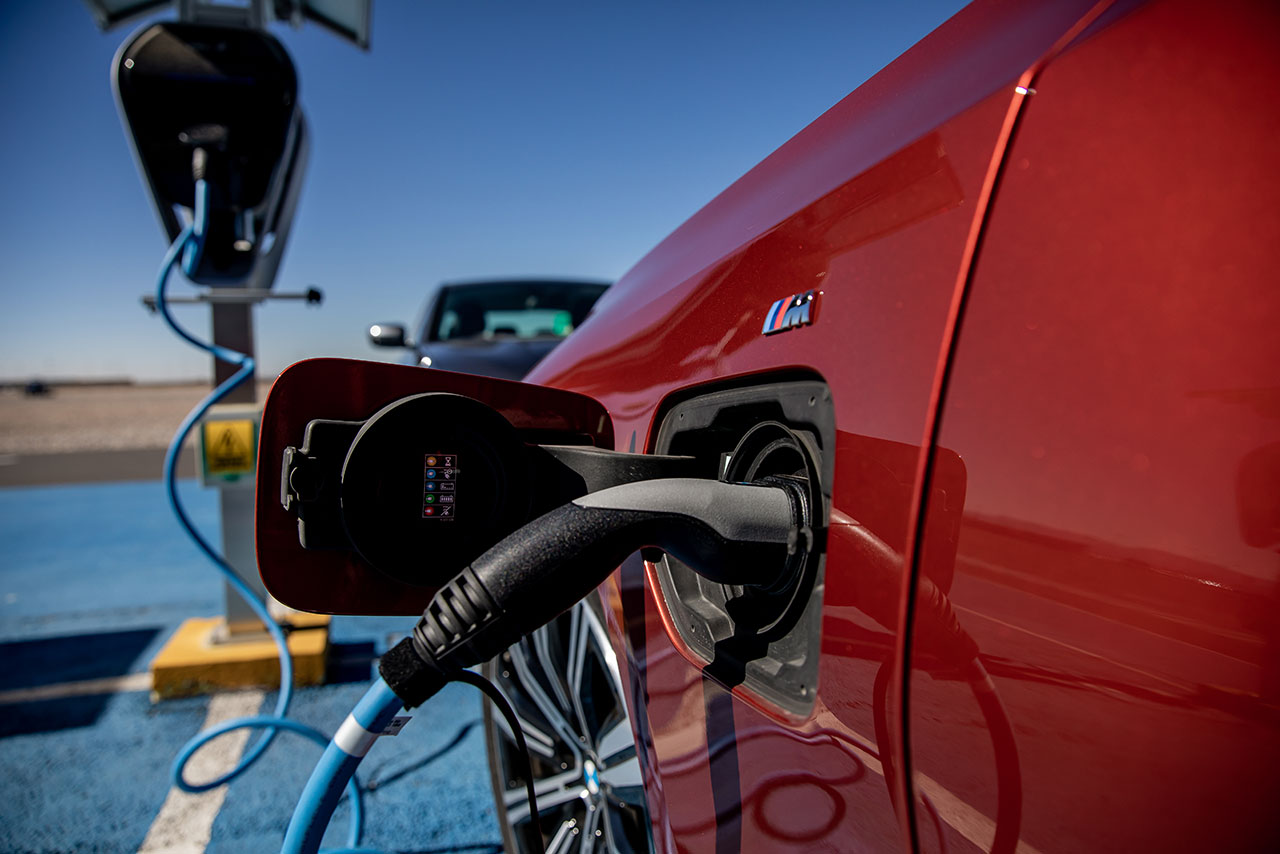
The drive of the BMW 3 Series PHEV comprises a four-cylinder petrol engine with TwinPower Turbo technology and an eight-speed automatic transmission with an integrated electric motor. The main advantage of this hybrid technology is that it offers more output than the conventional BMW 3 Series but is still more fuel-efficient.
The electric drive in the BMW 330e offers fully electric driving at up to 140 km/h with zero local emissions and a maximum electric range of 60 kilometres.
Shenyang
The BMW Brilliance Powertrain Plant first started producing high-voltage batteries in 2017. The next quantum leap came shortly after, in 2020, when the Battery Centre II was launched, doubling production capacity. The new facility was the first in the BMW Group production network to manufacture Gen5 high-voltage batteries, which power vehicles such as the brand-new BMW iX3. By the middle of 2021 the 100,000th high-voltage battery is expected to roll off BBA’s production lines.
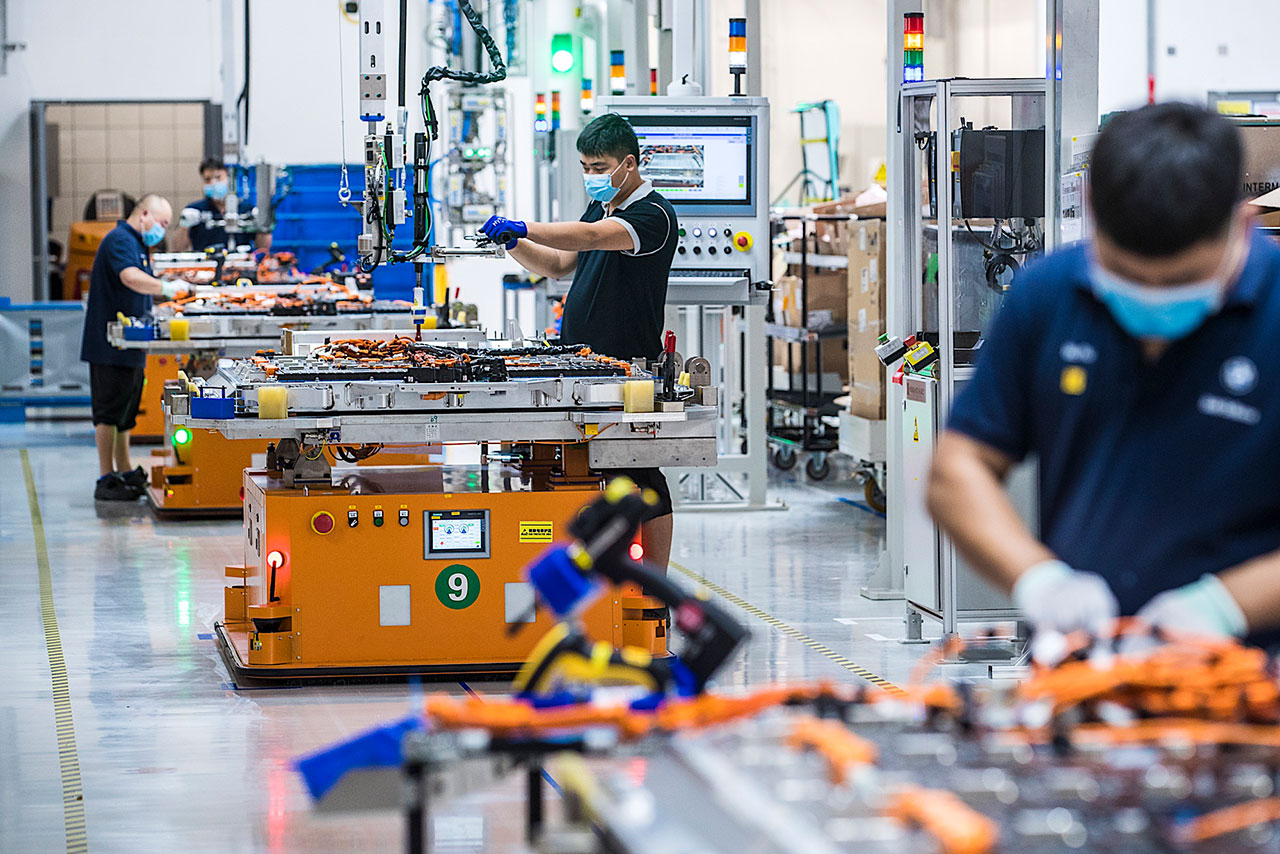
Spartanburg
In 2020 BMW Group Plant Spartanburg delivered two record-breaking plug-in hybrid models: output of the BMW X3 xDrive30e reached almost 23,000 units, and the BMW X5 xDrive45e clocked up over 24,000 units. These 47,000-plus electrified BMWs accounted for 13 percent of total output from Plant Spartanburg.
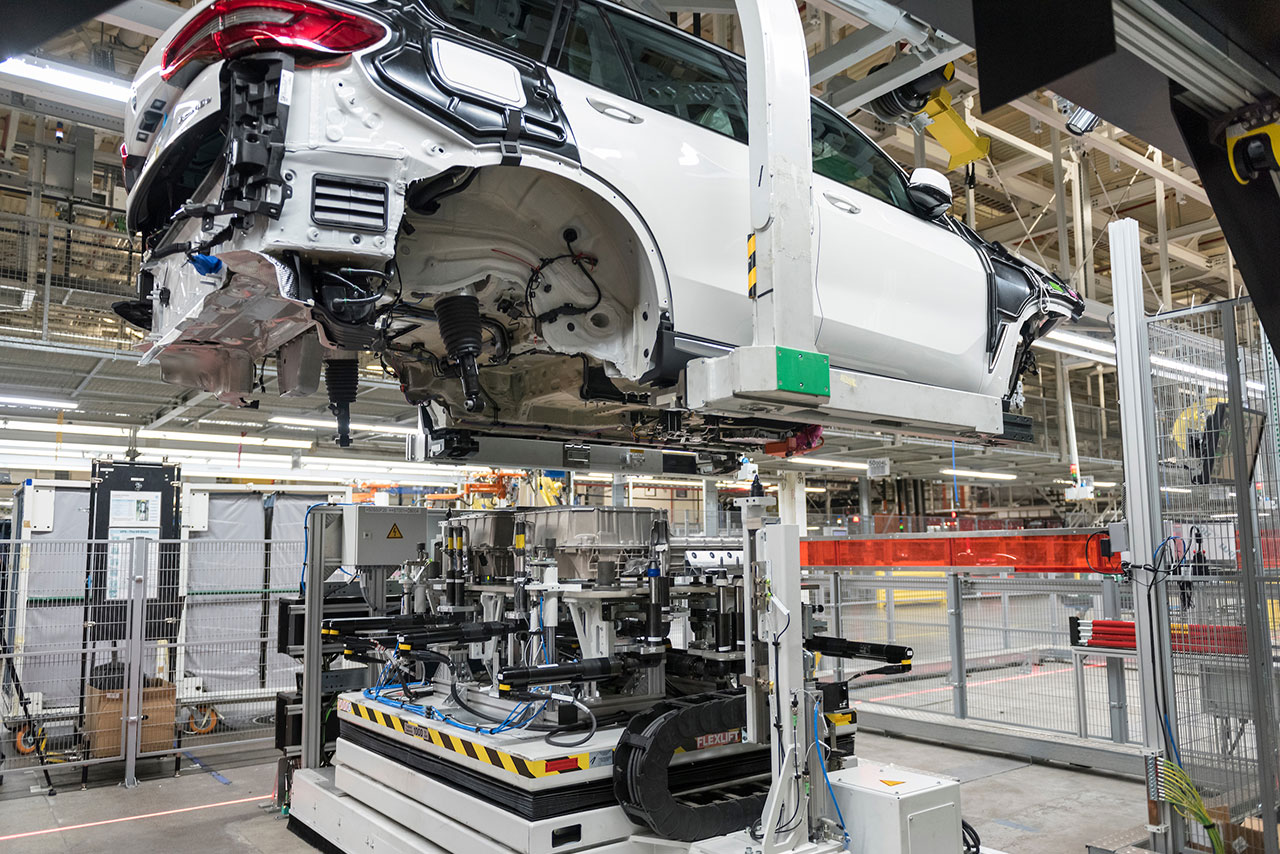
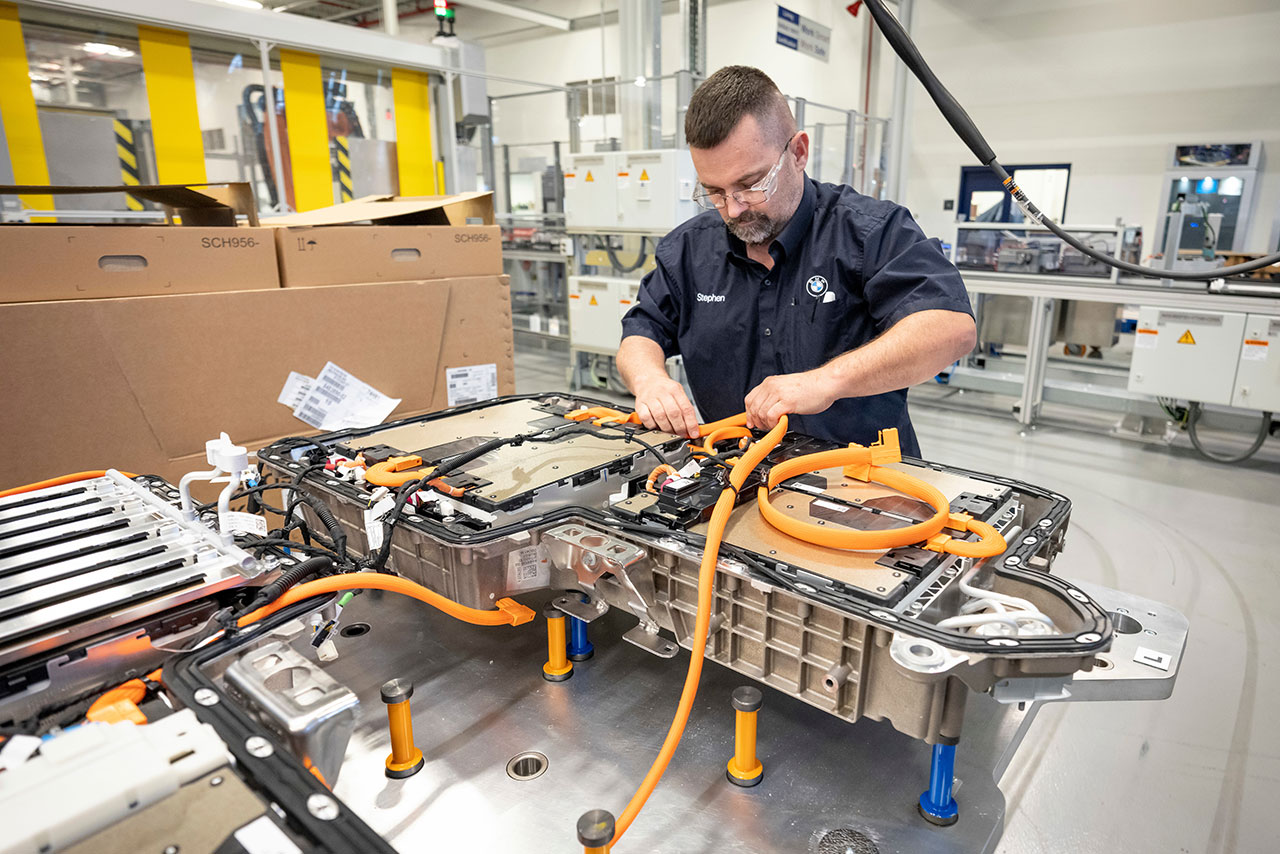
It was all made possible by the extension in 2019 of high-voltage battery production. Spartanburg has been assembling high-voltage battery packs for electrified vehicles since 2015, making the BMW Group a pioneer of electromobility in the US as well.
Steyr
BMW Group Plant Steyr develops and manufactures numerous components for electromobility. Its technological prowess is evidenced in the BMW iX3, iX and i4, among others.
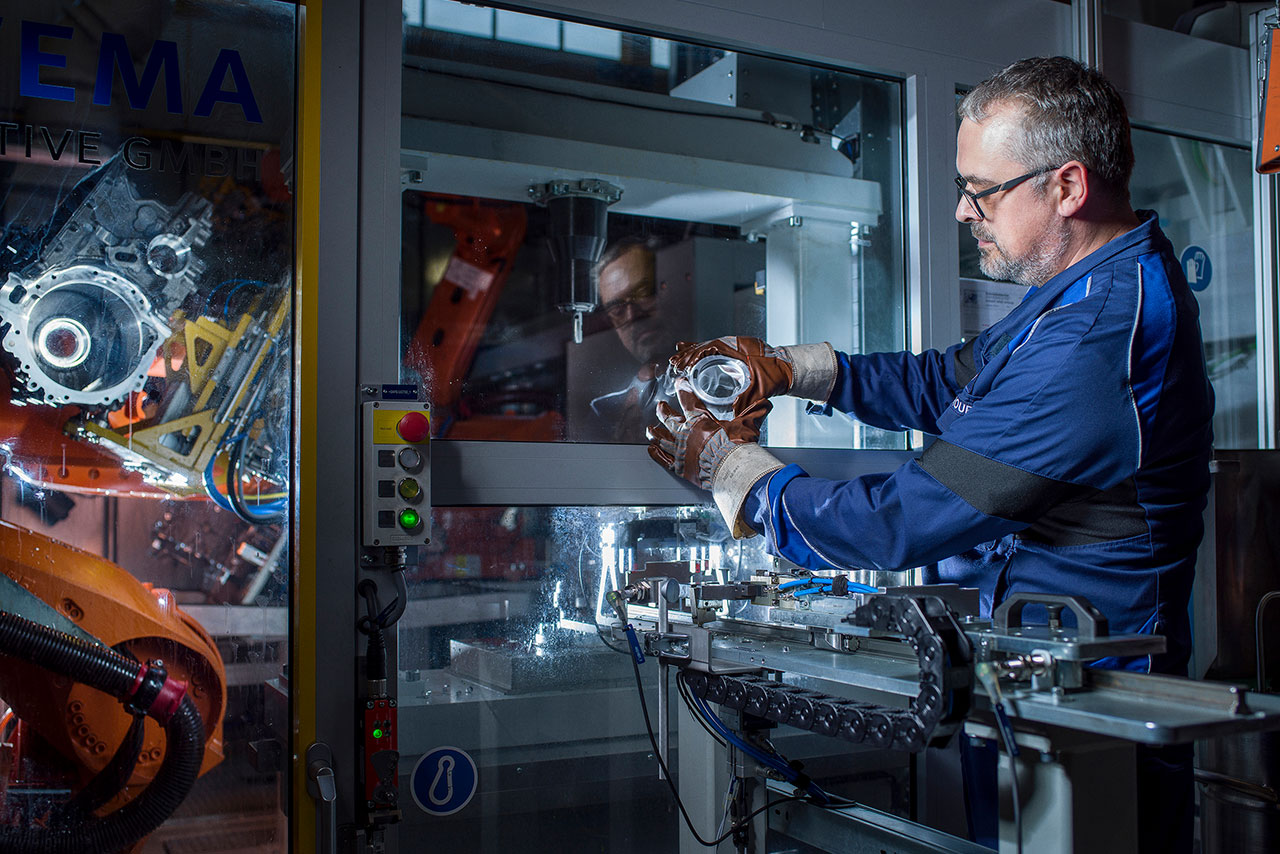
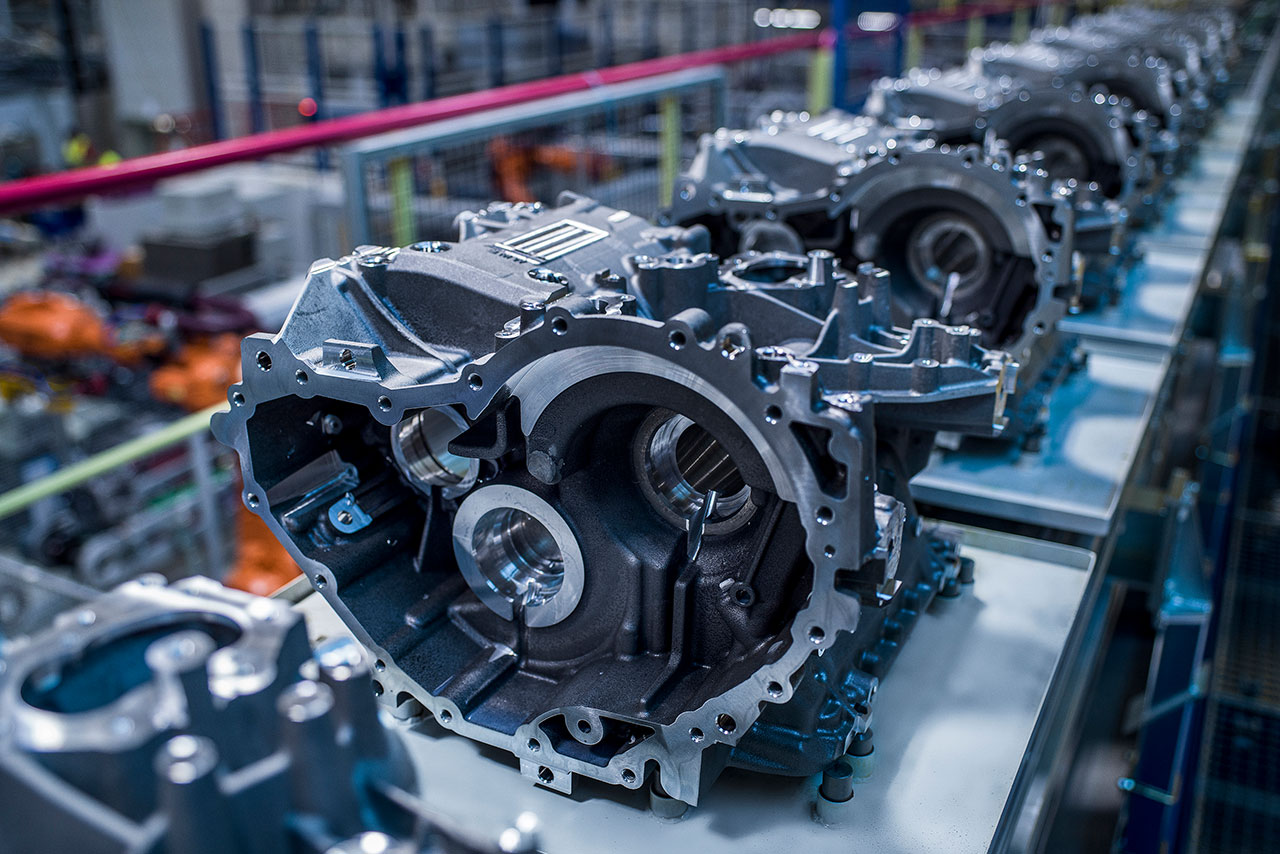
Steyr’s engine plant produces about a quarter of the BMW Group’s hybrid engines, and since last year Mechanical Production has be manufacturing the casing of the highly integrated Gen5 e-drive. The team in Development work not only on our fuel-efficient combustion engines but also our alternative drives. In addition the cooling cycles for our all our new battery-electric vehicles are developed and trialled in Steyr, where about ten percent of the Development Centre team are already dedicated to electromobility.