The BMW Group Recycling and Dismantling Centre is not only Germany’s biggest recycling centre. It acquires new recycling-knowledge while taking apart pre-series vehicles to achieve maximum efficiency.
The end of a vehicle’s life is not a sight for car lovers, especially if they have weak nerves: metal groans, glass shatters. An excavator goes into action, its steel grapple grabbing at the engine block. A jerk, a few flying parts, and what was once the heart of a BMW vehicle hangs in the air.
But it doesn’t stop there. The excavator changes tools. It rips the roof of the car open and tears out the leather seats, the upholstery, the instrument panel. Then, with almost surgical precision, the excavator seizes the front of the wiring harness and rolls up the multicolor tangle of cables until the bundle dangles beneath the excavator arm.
In this nondescript industrial estate in the Munich suburb of Unterschleißheim up to 10,000 cars undergo this treatment every year – making it Germany’s biggest car recycler. The BMW Group Recycling and Dismantling Centre (RDC) has been here since 1994, mainly dismantling pre-series vehicles, one-offs from testing and development that are not authorized for sale, tearing them to pieces and recycling them in the brightly lit workshops.
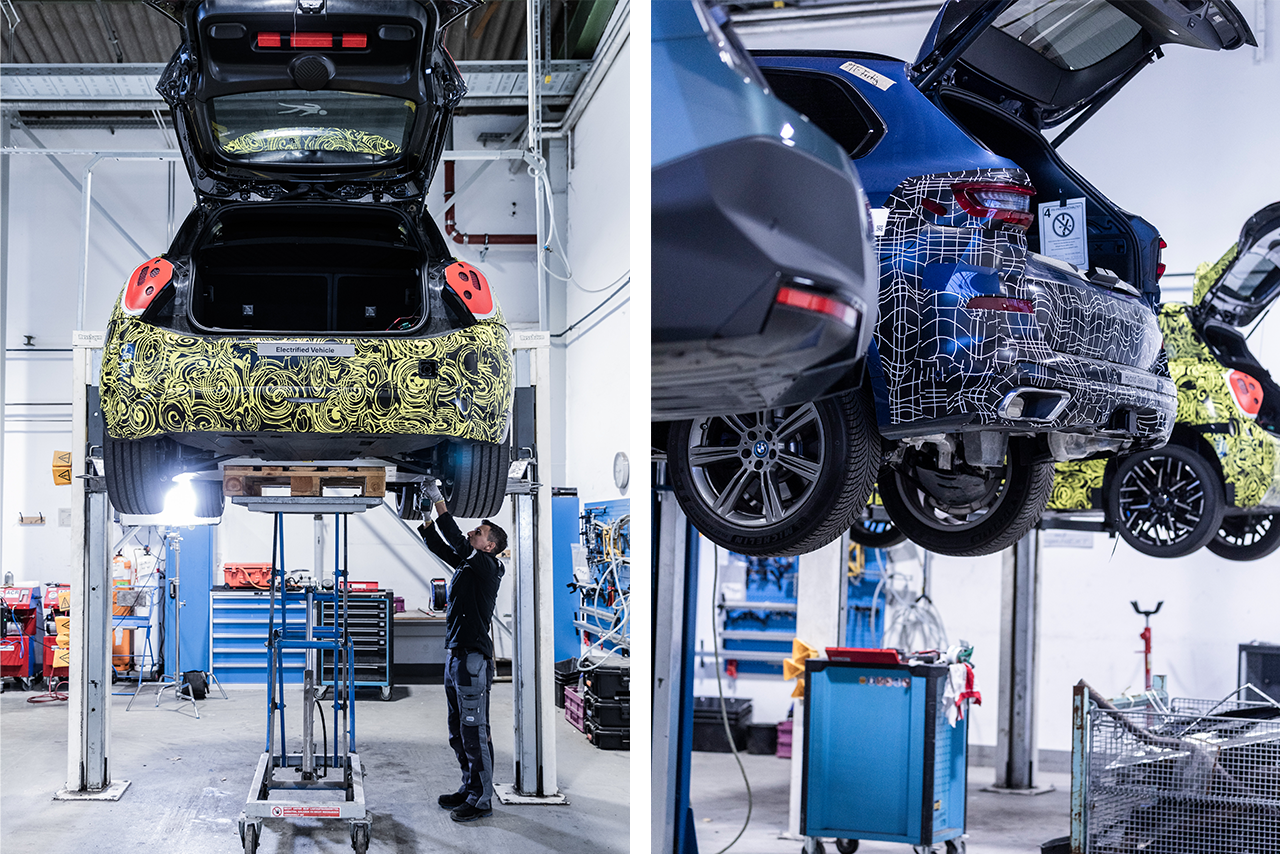
How to recover three kilometers of copper cable from one vehicle
In the context of the circular economy, however, the Centre doesn’t just tackle recycling, but also the end-of-life stage of cars. How can they be recycled more quickly, more efficiently and more valuable in future and how do they need to be designed to enable the maximum possible number of their components to be reused, repaired or remanufactured. Modern vehicles contain between one and a half and three kilometers of cable alone, all mainly valuable copper. Other parts are rich in aluminium, the catalytic converter contains platinum, rhodium and palladium. All of these parts can be recycled. The BMW Group gains valuable knowledge on how to make the recycling process more efficient.
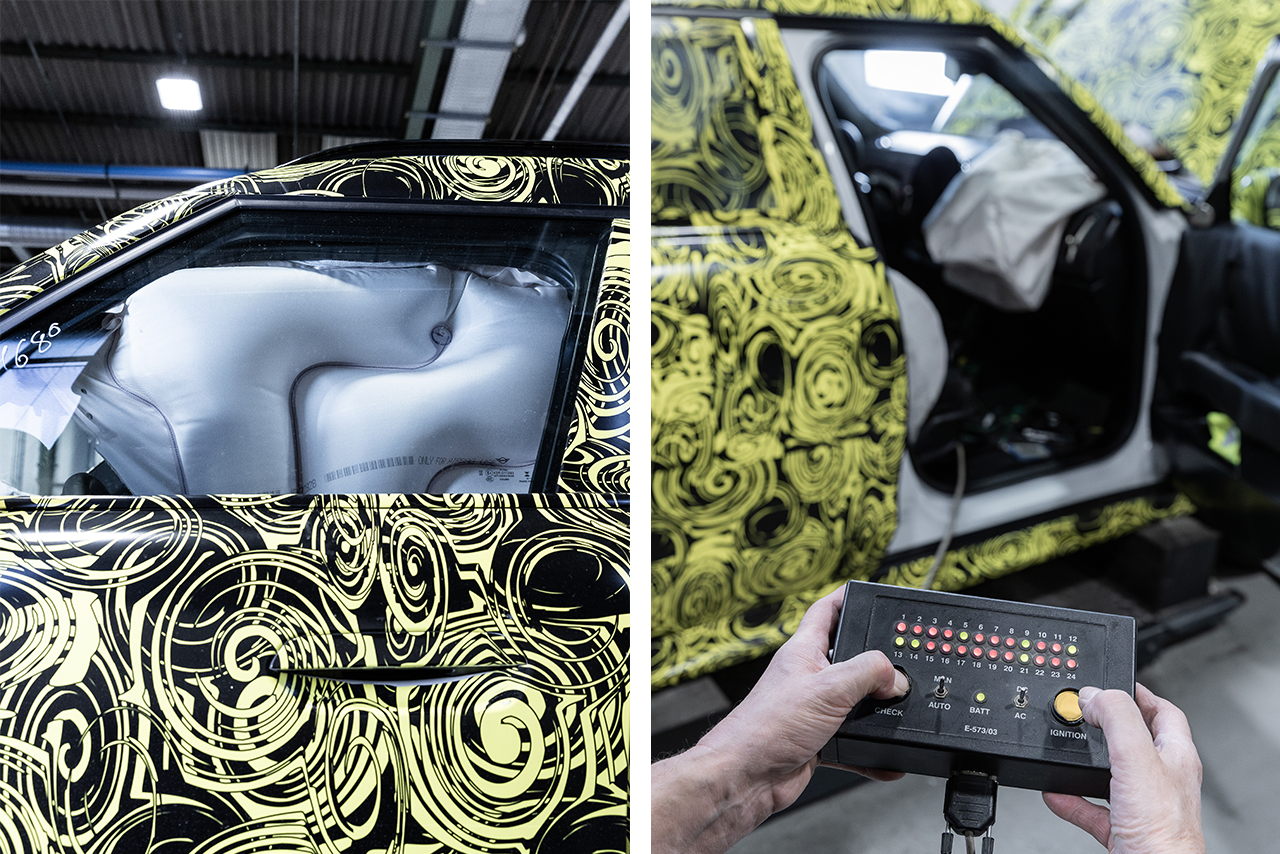
Special tools for specific tasks so that nothing is wasted
Once the high-voltage battery has been removed from vehicles with an electric drive for further recycling, it's time to get down to business: A loud bang. First, experts ignite the front airbags, then the ones on the side, then the seatbelt tensioners and finally the battery terminal. The interior of the car is full of smoke, there is a smell of fireworks. The pyrotechnics found in all vehicles have now been neutralized, as required by law. The RDC developed a special tool for this. Finally, all the fluids are removed – oil, wiper fluid, brake fluid, coolant. All fluids are reused within the RDC.
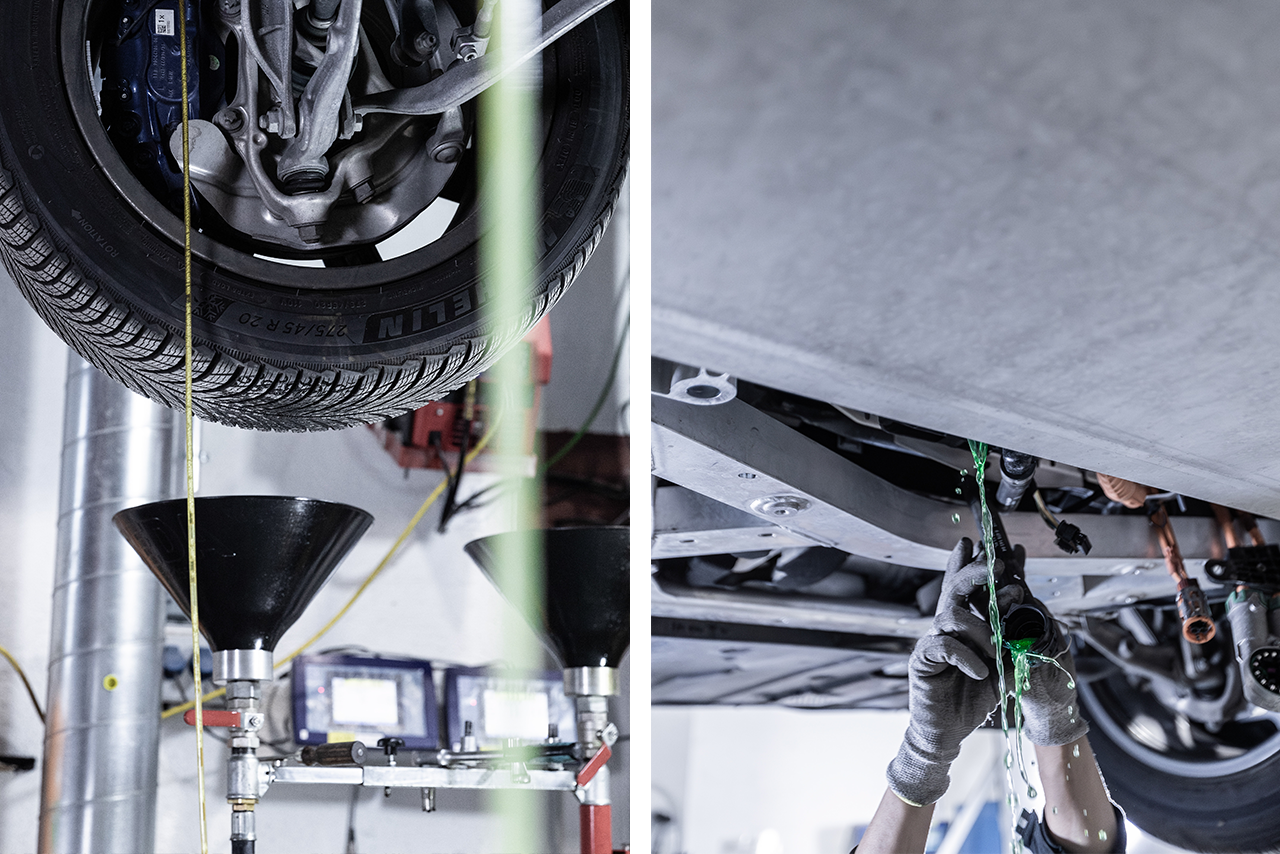
What is now left of the vehicle ends up in an orange scrap press. More splintering, crunching, groaning. Even the floor vibrates under the 300-tonne press force. All that remains is a cube the size of a fridge. This will be sent to an external recycling company for shredding: there, most of the materials contained in it will be shredded, separated, cleaned, melted down in further recycling steps, and finally returned to their secondary material cycles. With the creation of the metal cube, the carmaker has met its obligations. By law, 85 per cent of a vehicle must be recyclable and a full 95 per cent must be recoverable, which also includes thermal recycling.
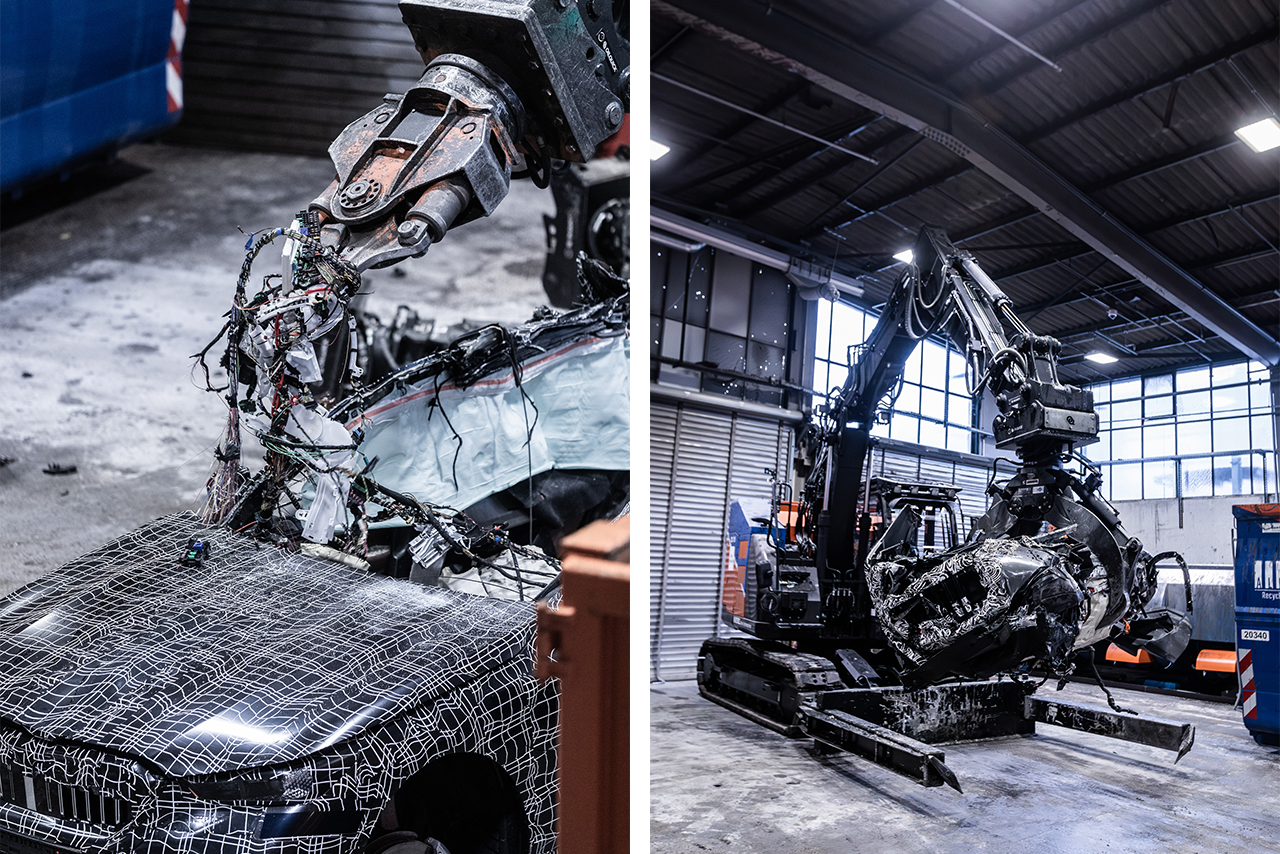
Sharing the knowledge with 3,000 recyclers worldwide
The main purpose of the RDC is to find the most efficient and quickest ways to recycle vehicles at the end of their useful lives – in about 21 years, on average. The steps required for this are logged in a cross-manufacturer database to which 3,000 recyclers in 41 countries have cost-free access. These businesses are absolutely essential if the circular economy is to work: recyclers need to be able to remove the usable parts and recover as many materials as possible, with the least possible effort and expense. Cost and the ability to identify material composition remain the most important factors in the recycling process.
Cost or sustainability? This is the question that Alexander Schüll, manager of the RDC, wants to move on from. “We need to abandon that debate and be absolutely clear about the fact that sustainability is both the key and the starting point for progress towards systemic change. Only then will we have genuinely circular thinking.”
Only a circular mindset will succeed
This is why the RDC offers guided tours of the RDC – not least for staff in other BMW Group departments, who have to learn more about the importance of the recycling center and its various circular approaches. “Only if we take a circular approach to product development, if the mindset is circular, then we can achieve a good, sustainable, holistic solution,” says Schüll.